驚くほどに多くの大小さまざまな部品を精密にあわせていくことで1本のメタル(チタンほかの金属製)眼鏡が生まれます。部品を作るのに必要な金型はかなり高価で大きな機械装置も必要なことから工場が大きいのも特徴的。金属を扱うことから高圧・高温等、不慣れな人間にはより注意も必要となることからそのスケール感をお伝えできるような装置の写真撮影は控えましたが、メタル工場ならではのショットとあわせてその空気をお感じいただければと綴ります。
竹内光学
初めてのメタル工場視察は創業昭和7年の竹内光学さんで大変お世話になりました。「機械と人間さん」という言葉がとても印象的だった竹内会長自ら鯖江の眼鏡の歴史の講義と、広い工場内を歩いて一つ一つの工程を説明してくださったことはお陰様で大きな財産になりました。
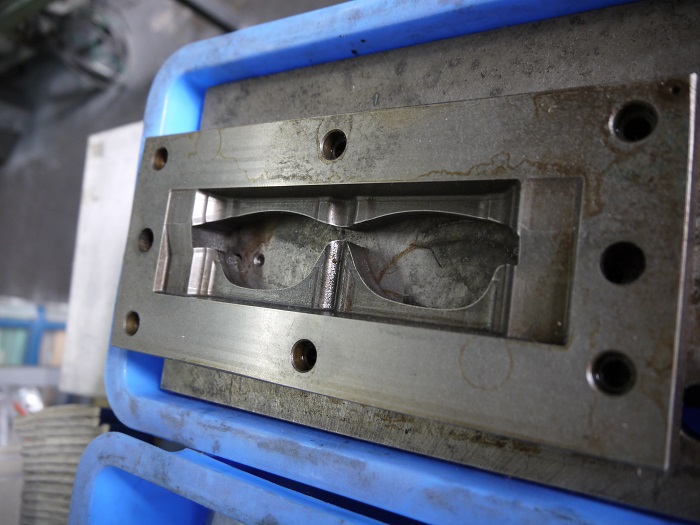
もしかすると地味に見えてしまうかもしれない1枚ですが、実はとても貴重でメタル素材の眼鏡ならではということでトップに採用しました。「車が買えてしまうよ」と言われるほどに高価な金型。その上、大小様々な部品も一つ一つに金型ありき、と知ればセル素材(プラスティック)の眼鏡に比べてお値段が高くなるのも納得いただけると思います。図面から機械的に作られるものでもなく、職人さんの目と手で微調整を加えながら完成させている様子を数年後、別の機会に見せていただいてさらにびっくり感動したことも忘れられません。
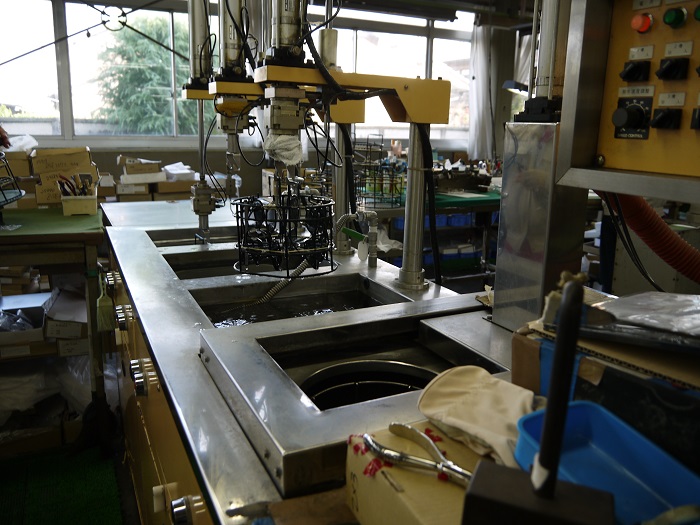
広い工場内では工程ごとに景色も大きく異なります。こちらは金属素材だけあって様々な工程で必須となる油を綺麗に落としているところです。
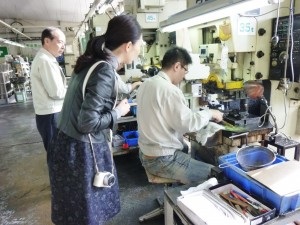
大きな機械が大半を占めていて作業されている人を探すくらいのエリアもあれば、こういった工程も。「機械に任せるところと、人だからの部分」メタル工場は人と、人が作った機械とが融合してできることの凄さを実感する場でもありました。
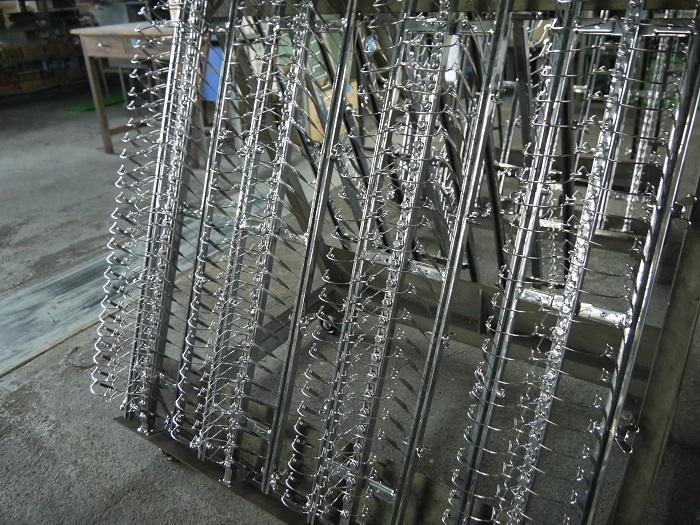
金属が数々の工程を経て眼鏡の形にどんどん近づいていく様子はワクワクするのと同じくらいに、これだけの手がかかっているのだと目の当たりにしたら背筋が伸びる思いでした。ネジ1本、小さな部品一つ、そのどれが欠けても眼鏡は完成しない・・・当たり前の事実の重みです。
浜本テクニカル株式会社
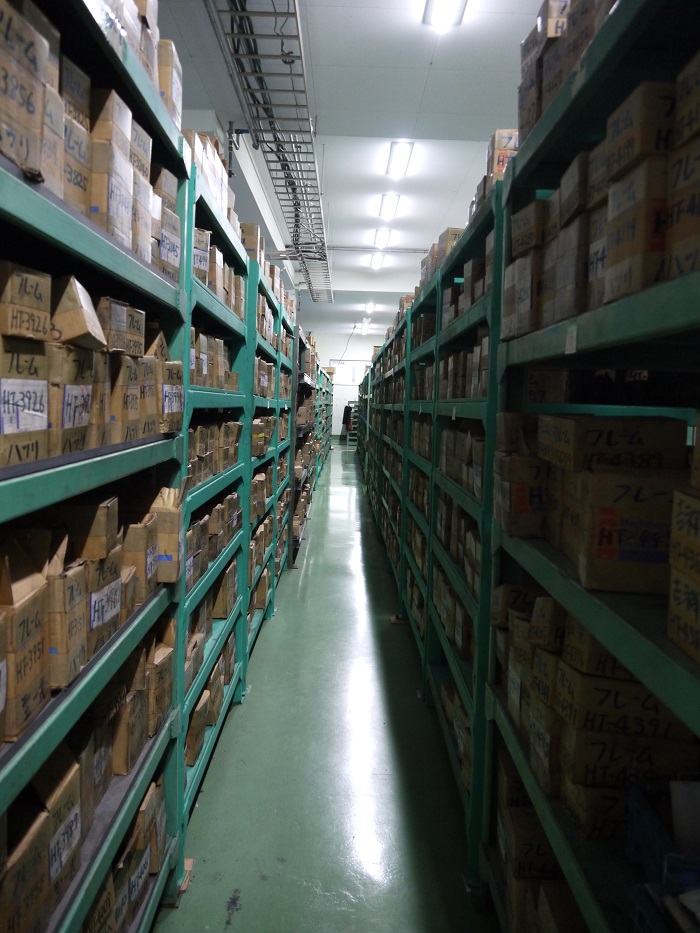
最初の(新作)生産のときだけでなく、同じモデルを作り続けるにはこれがなくては始まりません。とはいえ数も多くて一つ一つがずっしり重い!工場(ブランド)にとっては人と技術はもちろんのこと、この金型もとても大事な財産です。あまたの金型が歴史の証ともいえるほど広々と敷地を占めていました。
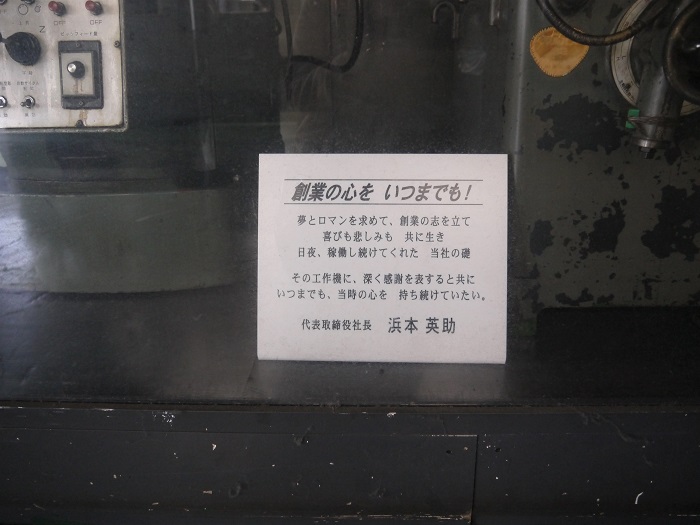
どれだけ大きな投資、覚悟だったのか・・・それは当時の鯖江の眼鏡業界を想像しながら工場視察の終盤に大きく響くものでした。愛と情熱が今でも滲んでいるようです。
lafont
フランスのメガネ産地ジュラへのファクトリーツアーでは、夜明け前のパリを経ち夜に戻るまでの丸1日、長年lafontを製造されている工場にお連れいただきオーナー自ら説明してくださるなど大変お世話になりました。(複雑な説明になると分かるか?と確認しながら進めてくださりお気持ちが本当にありがたかったです)ラファエルさんにも助けていただき理解を深めながら、各国のオプティシャンとご一緒できたことも素敵な経験になりました。
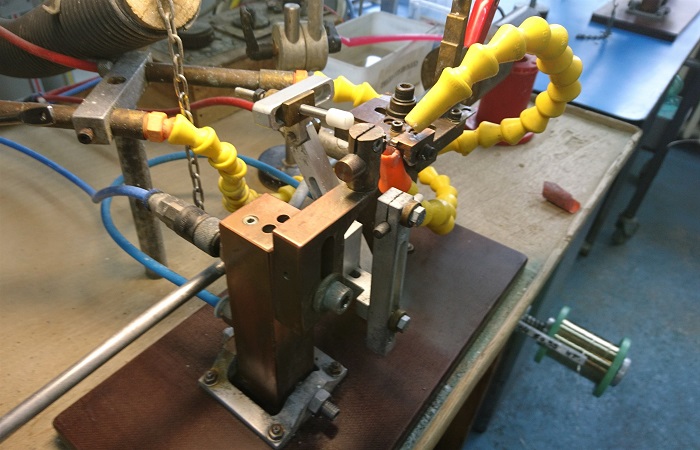
国は違えど作業の流れは基本同じというのは本当ですが、同じ作業でも工場によって少しずつ違うというのもしかり。治具(作業性を高めるための道具)がビジュアル的にもとっても魅力的だったのでご紹介します。

次に入る前の準備の工程で、筒状になっている部品(画面中央の黒*ホワイトの縦長の部品。アセテートと呼ばれるプラスティック製)の先端がダメージを受けないように、1本1本保護するためのキャップ状の部品をはめています。初めて見る私はあまりのキメ細かさに感動するばかり!1本の眼鏡は、言うなればこんな気配りの集合体だと思ったらお手持ちの眼鏡が益々愛おしく感じていただけるのでは、ということで沢山の写真のなかから結びの1枚にどうぞ。